Case Study: How We Improved Supply Chain Efficiency for a Local Business
To
Introduction
In today's fast-paced business environment, supply chain efficiency is crucial for maintaining a competitive edge. Recently, we had the opportunity to work with a local business to enhance their supply chain operations. This case study will explore the strategies we employed and the remarkable results achieved.
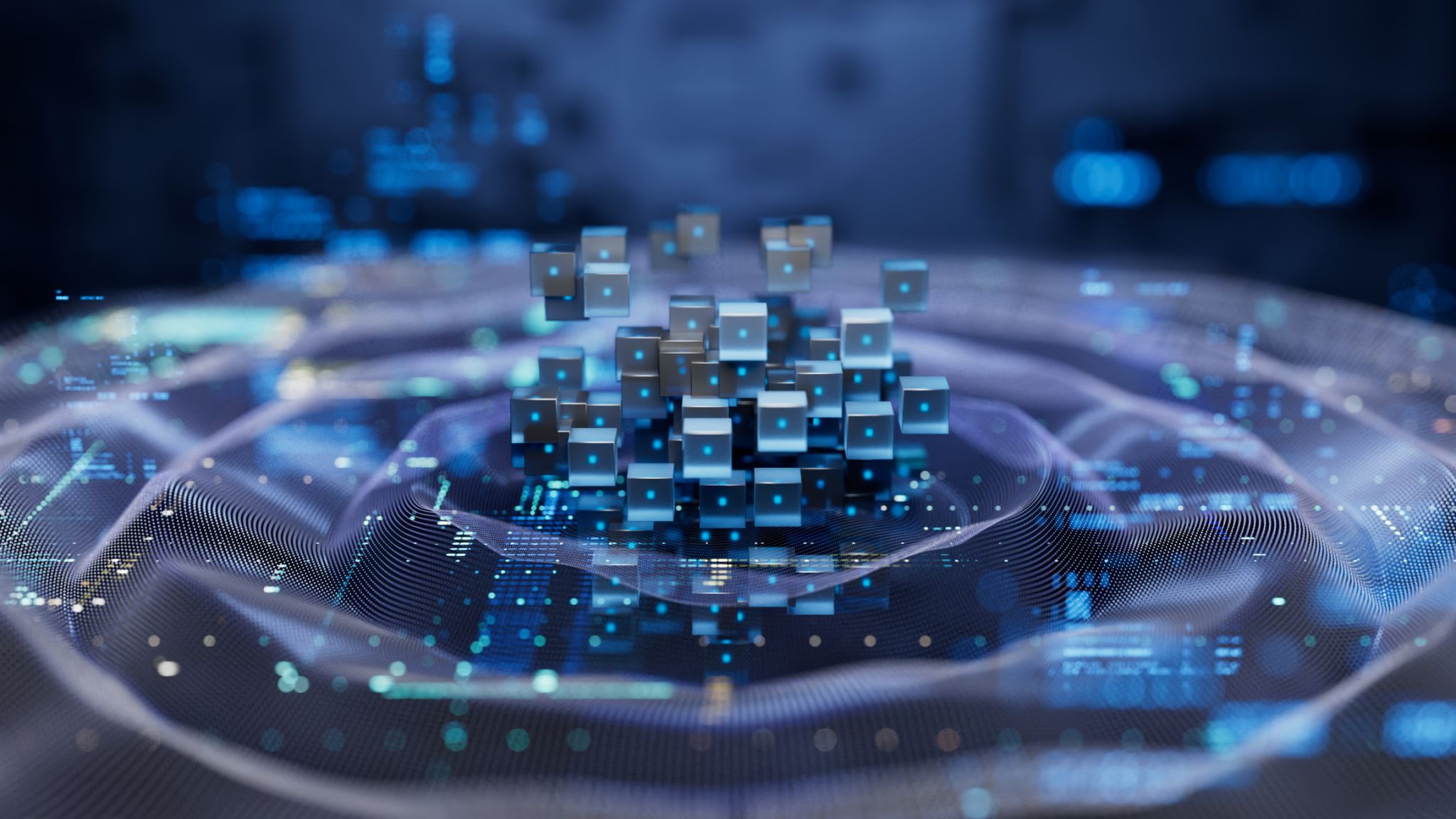
Understanding the Challenges
Our client, a mid-sized manufacturer, was experiencing delays and inconsistencies in their supply chain. These issues were impacting their production schedules and customer satisfaction levels. The primary challenges included:
- Inaccurate inventory levels
- Delayed shipments from suppliers
- Inefficient distribution processes
Developing a Tailored Strategy
To address these challenges, we began by conducting a comprehensive analysis of their existing supply chain operations. This involved reviewing their current processes, identifying bottlenecks, and understanding the limitations of their technology solutions. Based on our findings, we developed a customized strategy that focused on three main areas:
- Implementing an advanced inventory management system
- Improving communication with suppliers
- Streamlining distribution channels
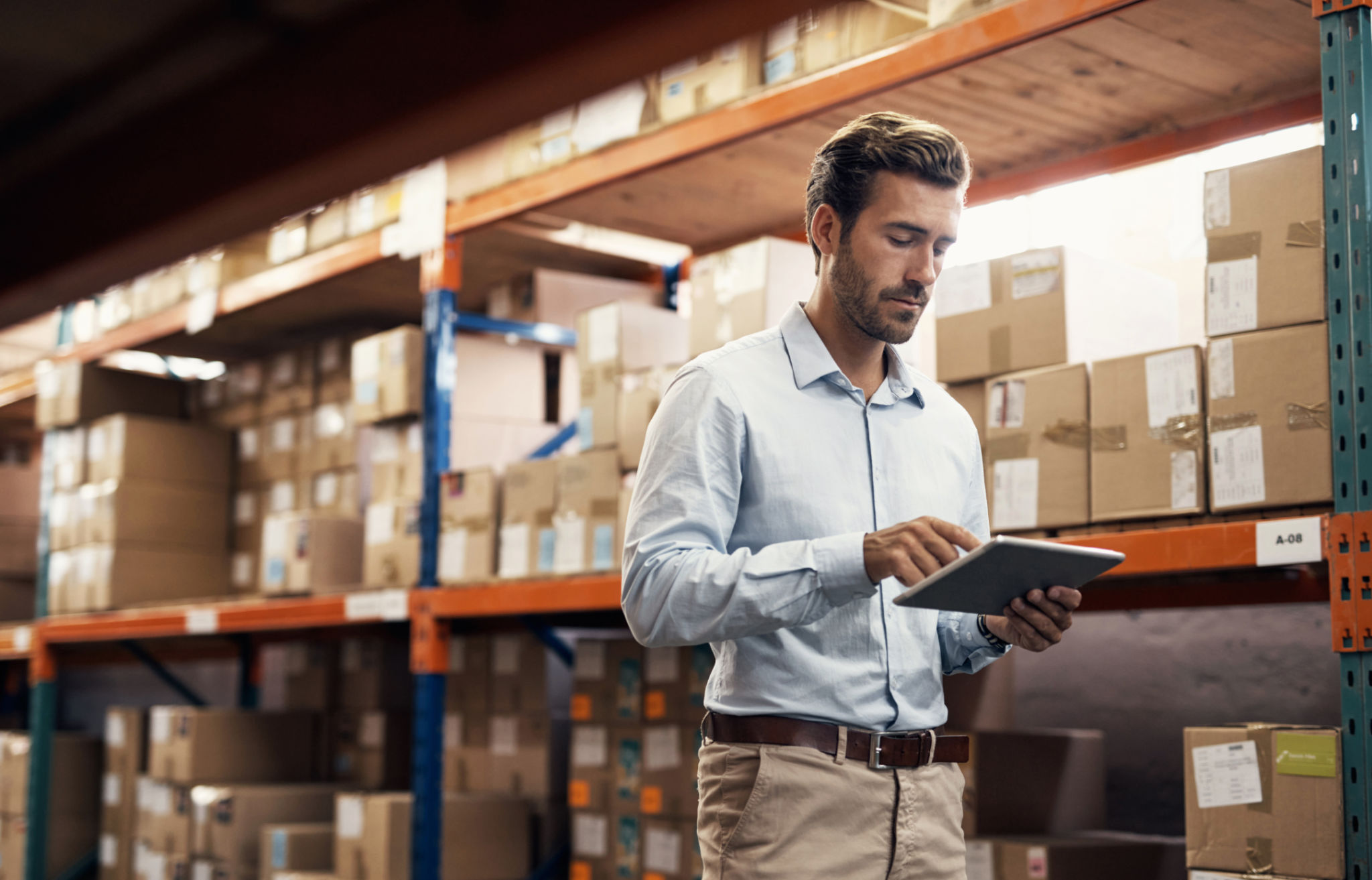
Implementing Solutions
The first step was to introduce an advanced inventory management system. This technology enabled real-time tracking of inventory levels, reducing discrepancies and ensuring optimal stock availability. By integrating this system with their existing ERP, we provided them with greater visibility and control over their stock.
Next, we worked on enhancing supplier relationships by establishing clear communication channels and setting expectations regarding delivery timelines. Regular meetings were scheduled to review performance and address any concerns promptly.
Streamlining Distribution Processes
For distribution, we focused on optimizing routes and reducing transit times. By analyzing historical data and using predictive analytics, we were able to devise more efficient routing plans. This not only minimized transportation costs but also improved delivery reliability.

Measuring Success
The impact of these changes was significant. Within three months of implementation, the business experienced:
- A 20% reduction in inventory holding costs
- A 30% improvement in order fulfillment speed
- A 15% decrease in transportation expenses
Customer satisfaction levels also saw a marked improvement, as delays and stockouts became less frequent.
Conclusion
This case study highlights how targeted interventions can drastically improve supply chain efficiency. By leveraging technology and fostering strong supplier relationships, businesses can achieve operational excellence and enhance their competitive advantage. If your organization faces similar challenges, consider adopting a strategic approach tailored to your unique needs.
With thoughtful planning and execution, it's possible to transform supply chain operations, leading to increased profitability and customer satisfaction.